Mastering Thermal Management in High Current PCB Design
High current PCB (Printed Circuit Board) design is a crucial aspect of modern electronics, especially for devices and systems that handle substantial power loads.
High current PCB (Printed Circuit Board) design is a crucial aspect of modern electronics, especially for devices and systems that handle substantial power loads. Effective thermal management is vital in these applications because excessive heat can degrade performance, reduce the lifespan of components, and even cause catastrophic failures. In this blog post, we will explore various strategies for managing heat in high current PCBs, ensuring optimal performance and reliability.
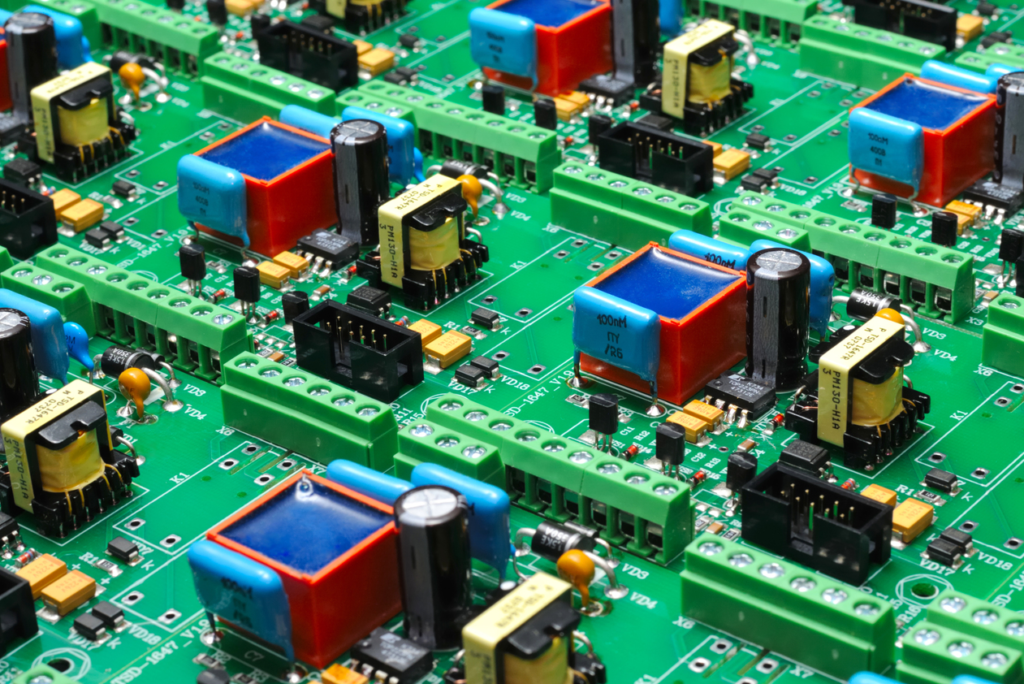
Understanding Heat Generation in High Current PCBs
Heat in high current PCBs is primarily generated by power components and the high current traces themselves. As current flows through the PCB, the inherent resistance of the materials causes heat to build up. This heat, if not managed properly, can lead to several issues such as component damage, signal degradation, and overall system failure. Understanding the sources of heat and the mechanisms behind its generation is the first step towards effective thermal management.
High current traces are particularly prone to heat generation due to their role in carrying large amounts of electrical current. The resistance of these traces, even if minimal, can produce significant heat when the current is high. Additionally, power components such as transistors, diodes, and integrated circuits also contribute to heat generation, further complicating the thermal management challenge.
Heat Dissipation Techniques
To address the heat generated in high current PCBs, various heat dissipation techniques can be employed. These techniques can be broadly categorized into conduction, convection, and radiation methods.
Conduction Methods
Conduction is the process of heat transfer through direct contact. In high current PCBs, this can be achieved by using thick copper layers and thermal vias. Thick copper layers enhance the PCB’s ability to conduct heat away from critical areas. By increasing the thickness of the copper, the PCB can handle higher current loads without overheating.
Thermal vias are another effective conduction method. These are small holes filled with conductive material, such as copper, that connect different layers of the PCB. They provide a path for heat to travel from the surface of the PCB to the inner layers or to a heat sink. Thermal vias are especially useful in multilayer PCBs where heat needs to be dissipated from densely packed areas.
Convection Methods
Convection involves the transfer of heat through a fluid, which can be either a liquid or a gas. In the context of PCB design, convection is usually achieved through air cooling. Heat sinks and fans are commonly used to enhance convection.
Heat sinks are passive devices that attach to components and increase the surface area available for heat dissipation. They work by conducting heat away from the component and then dissipating it into the surrounding air. Fans, on the other hand, actively move air across the PCB, helping to carry away heat more efficiently. Forced air cooling with fans can significantly reduce the temperature of high current components, ensuring they operate within safe limits.
Radiation Methods
Radiation is the transfer of heat through electromagnetic waves. While it is not the primary mode of heat dissipation in PCBs, it can still play a role in overall thermal management. Heat spreaders and thermal pads are examples of radiation methods.
Heat spreaders are used to distribute heat over a larger area, making it easier to dissipate. They are typically made of materials with high thermal conductivity and are placed on top of heat-generating components. Thermal pads and interface materials improve the thermal connection between components and heat sinks or heat spreaders, ensuring efficient heat transfer.
PCB Design Considerations for Thermal Management
Effective thermal management starts with good PCB design. Several design considerations can help manage heat more effectively, ensuring the PCB performs reliably under high current loads.
Trace Width and Thickness
The width and thickness of traces are critical factors in managing heat. Wider and thicker traces have lower resistance, which means they generate less heat for a given current. Designing traces with appropriate width and thickness can significantly reduce the overall heat generated in the PCB.
PCB Layout Strategies
The layout of the PCB plays a crucial role in thermal management. Proper component placement and thermal zoning can help distribute heat more evenly across the board. Thermal zoning involves grouping components based on their thermal characteristics, keeping high-power components separate from more heat-sensitive areas. This approach helps prevent hotspots and ensures more uniform heat distribution.
Layer Stack-Up Configuration
The configuration of the PCB’s layers can also impact thermal management. Multilayer PCBs provide more paths for heat to travel, improving overall heat dissipation. Thermal isolation techniques, such as using dedicated thermal layers or placing heat-generating components on specific layers, can further enhance thermal performance. These strategies help keep hot and cold areas separate, reducing the risk of overheating.
Advanced Thermal Management Solutions
For applications with extreme thermal requirements, advanced thermal management solutions may be necessary. These solutions often involve more sophisticated techniques and materials to ensure effective heat dissipation.
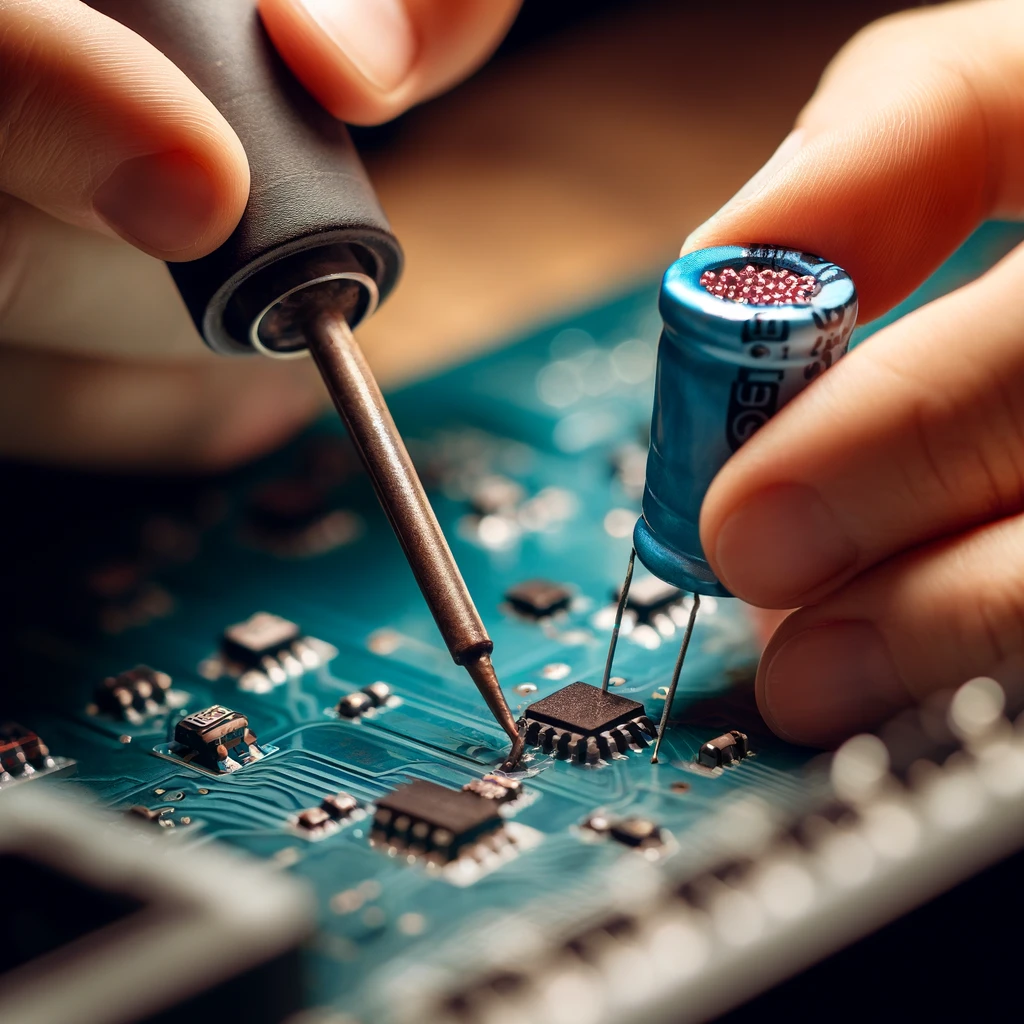
Embedded Heat Pipes
Embedded heat pipes are a highly efficient method for transferring heat. These small tubes contain a fluid that evaporates at one end (the hot end) and condenses at the other (the cool end), effectively transferring heat away from critical areas. Embedded heat pipes can significantly enhance thermal performance in high current PCBs, especially in compact designs where space is limited.
Liquid Cooling Systems
In some high-power applications, air cooling may not be sufficient to manage heat. Liquid cooling systems can be used to provide more effective thermal management. These systems circulate a liquid coolant through the PCB, absorbing heat and carrying it away to a radiator or heat exchanger. While more complex and costly than air cooling, liquid cooling systems can handle much higher heat loads, making them suitable for demanding applications.
Advanced Materials
Using advanced materials with high thermal conductivity can also improve heat management. Thermal interface materials (TIMs) and high thermal conductivity substrates are examples of such materials. TIMs improve the thermal connection between components and heat sinks, while high thermal conductivity substrates enhance the overall heat dissipation of the PCB. These materials can be especially useful in applications where traditional cooling methods are insufficient.
Thermal Simulation and Analysis
Thermal simulation tools are essential for designing high current PCBs. These tools allow designers to model how heat will flow through the PCB and identify potential hotspots. By analyzing simulation results, designers can make informed decisions to improve thermal performance.
Thermal simulation tools provide detailed insights into the thermal behavior of the PCB. They can predict temperature distribution, identify critical areas that require additional cooling, and evaluate the effectiveness of different thermal management strategies. By using these tools early in the design process, designers can optimize the PCB layout, component placement, and cooling methods to ensure reliable performance under high current loads.
Real-World Applications and Case Studies
High current PCBs are used in various industries, each with unique thermal management challenges. Let’s look at some real-world applications and how thermal management is addressed in these scenarios.
Automotive Industry
In the automotive industry, high current PCBs are used in electric vehicles (EVs) and other high-power applications. Effective thermal management is crucial to ensure the reliability and safety of these systems. For example, power electronics in EVs generate significant heat, which must be managed to prevent overheating and ensure efficient operation. Advanced cooling methods, such as liquid cooling and embedded heat pipes, are often used to handle the high thermal loads in automotive PCBs.
Aerospace and Defense
The aerospace and defense industries also require high current PCBs that can handle extreme temperatures and power loads. These applications often involve harsh environmental conditions, such as high altitudes and rapid temperature changes. Effective thermal management is essential to ensure the reliability of aerospace and defense systems. Advanced materials and cooling methods, such as heat pipes and thermal interface materials, are commonly used to manage heat in these applications.
Consumer Electronics
In consumer electronics, high current PCBs are used in devices such as smartphones, laptops, and gaming consoles. These devices require efficient thermal management to maintain performance and extend the lifespan of components. Heat sinks, thermal pads, and advanced materials are often used to dissipate heat in consumer electronics. Additionally, compact and efficient cooling methods, such as micro heat pipes, are becoming increasingly popular to manage heat in small, high-power devices.
Industrial Power Systems
Industrial power systems, such as power supplies and motor drives, also rely on high current PCBs. These systems often operate in demanding environments and require robust thermal management to prevent downtime and failures. Effective cooling methods, such as forced air cooling and liquid cooling, are commonly used in industrial power systems. Proper PCB design and advanced materials also play a crucial role in managing heat in these applications.
Standards and Testing for Thermal Management
To ensure the reliability of high current PCBs, various industry standards and testing methods are used. Thermal performance standards provide guidelines for designing PCBs that can handle specific heat loads. These standards help ensure that PCBs meet the required thermal performance criteria for different applications.
Thermal testing methods, such as thermal cycling and thermal shock testing, are used to verify that a PCB can handle the expected heat loads. These tests simulate real-world conditions, exposing the PCB to temperature variations and thermal stress. By conducting thorough thermal testing, designers can ensure that their PCBs will perform reliably under various thermal conditions.
Future Trends in Thermal Management
The field of thermal management is constantly evolving, driven by advancements in technology and increasing power demands. Emerging technologies, such as new cooling methods and advanced materials, are continually being developed to improve thermal performance.
The integration of IoT (Internet of Things) for real-time thermal monitoring is one such trend. IoT-enabled sensors can provide real-time data on the temperature and thermal performance of PCBs, allowing designers to make adjustments and optimize cooling methods dynamically. This approach can significantly enhance the efficiency and reliability of thermal management systems.
Advances in material science are also paving the way for more efficient thermal management solutions. New materials with higher thermal conductivity and better thermal properties are being developed, providing more options for managing heat in high current PCBs. These materials can help improve the overall thermal performance of PCBs, making them suitable for more demanding applications.
PCBs with PCBWay
PCBWay is a leading provider of printed circuit board (PCB) prototyping, manufacturing, and assembly services. They offer a comprehensive range of PCB-related services including fabrication, assembly, design, and stencil creation. Through their online platform, customers can upload design files, obtain instant quotes, and place orders for PCB prototyping and manufacturing. PCBWay also has a team of engineers available to provide design reviews and technical support.
Beyond PCB services, PCBWay offers additional services such as 3D printing, CNC milling, and laser cutting. Known for their competitive pricing, quick turnaround times, and high-quality products, PCBWay serves a diverse clientele spanning aerospace, medical, automotive, and consumer electronics industries.

The PCBWay Project Community is an online platform dedicated to electronics enthusiasts, hobbyists, and professionals, managed by PCBWay. It provides a space for members to connect, share knowledge, and showcase their electronics projects. The community features a forum for Q&A, a blog for sharing projects and experiences, and a project gallery for showcasing work. It also hosts various contests and challenges to foster innovation and creativity in electronics, with opportunities for members to win prizes.
Additionally, the PCBWay Project Community offers numerous resources and tools to aid members in their projects, including tutorials, design files, and PCB layouts. This community is an invaluable resource for anyone interested in electronics, providing a collaborative platform for learning, sharing, and innovation.
Conclusion
Thermal management is one of the critical important aspects of high current PCB design. By using effective heat dissipation techniques, optimizing PCB design, and leveraging advanced solutions and simulations, designers can ensure their PCBs perform reliably even under high current loads. As technology continues to advance, so too will the strategies and tools available for managing heat in high current PCBs. This continuous innovation will ensure that electronic devices can keep up with increasing power demands, providing reliable and efficient performance in a wide range of applications.